From time to time, I end up typing a ridiculously long email explaining some concept or another. Granted, I could be tested for some disorder that may lead to an explanation for this, but until then, I’ll post my musings in this blog so others can deliberate about my current mental state. Here’s one for example:
————————————————————————————
. . . . . .Let me give you some input as to why others use gravity metering for measuring energy usage in shared steam applications:
First off, gravity metering technology dates back to 1904 and Cadillac Meter, formerly of Detroit, MI. That’s a long time for any metering technology to be used, so the track record is pretty proven. To my knowledge, the only other metering technology to survive intact longer is the natural gas diaphragm meters that are strapped to the side of virtually every house in the US. If I remember right, they date back to 1846. Anyway, I digress.
Here’s a 3D on a G-sized measuring element:
Widely varying turndowns between summer and winter flows are best measured with gravity meters, as our turndown is in essence, infinite. Gravity is the only meter out there that can do that. All other metering techniques require velocity, so pumping equipment and electricity may be a factor in long term cost. Many returns are gravity fed, but if you are a pumped return, it’s a horse apiece as the gravity meter will feed an accumulation tank for pumping.
Typical maintenance on a gravity meter vs a turbine meter requires only a recommended change of bearings every 4 years, but we see people who regularly run these meters 10+ years with no degradation in performance. Bearing cost is about $20.00. Gravity will typically run as accurate at the start of 10+ years as at the end, finally stopping totally when the bearings give out and the meter stops turning. But the powerhouse will know right away, as they get real suspicious when the readings stop.
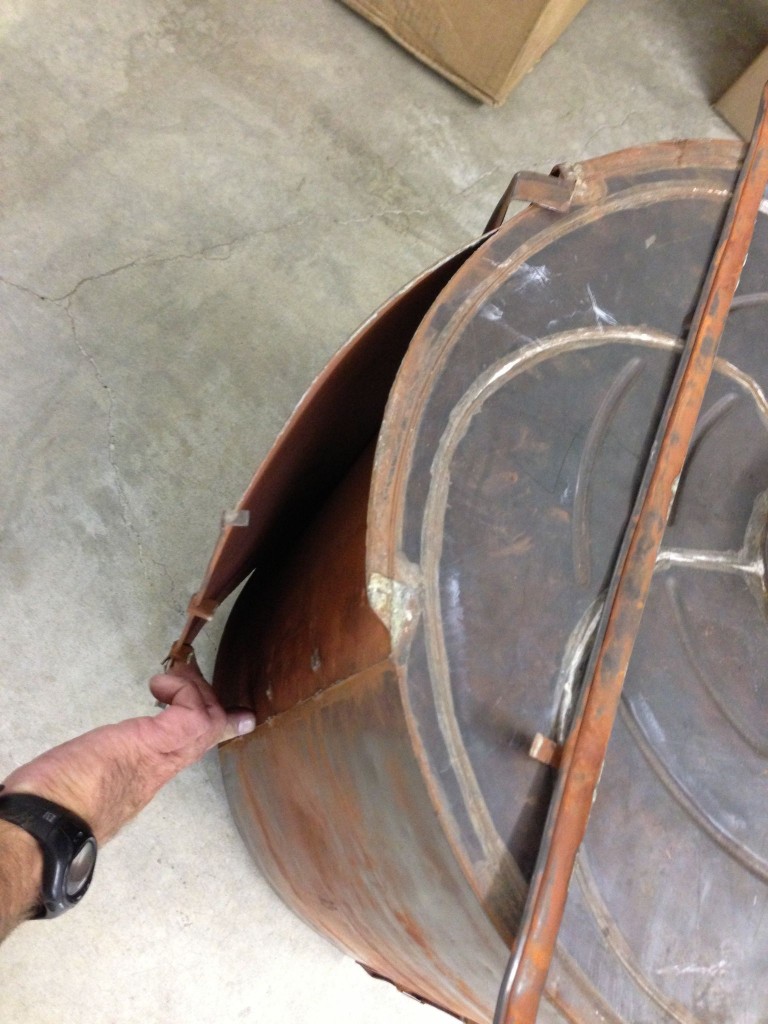
Another factor that now comes in play is the fact that almost all gravity meters are made out of stainless steel with welded joints. Original gravity meters were soldered together from sheet copper, and the main source of failure with these meters is failure of the soldered joints. With welded joints, these meters are virtually indestructable, and calibration is frozen to the original delivered spec. Aging does not change calibration, failed seams do, and the calibration almost always sways to the side of the customer, not the utility.
But it’s hard to make a blanket statement, isn’t it? Bent sides can also affect a calibration. This meter will report short for the customer. 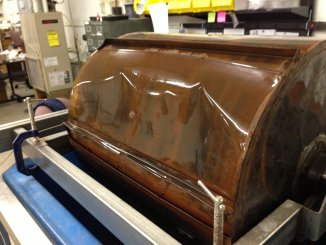
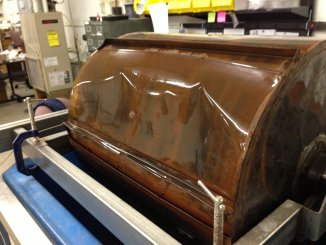
With all welded meters, the possiblility of splitting a seam is elimintated. In addition, we build our meters with a rim so that when placed on it’s side during maintenance, the drum walls are less likely to contact the floor. This helps to keep the calibration protected. The drum walls on “C” and larger drums are 24 gauge, and so are incredibly tough as well. But truth be told, if you try hard enough, you can dent a meter.
We provide Niagara turbine meters for condensate as well, and Siemens magnetic meters when they might apply. Turbine meters run 3-5 years, and are then typically thrown away, as maintenance is well over half the cost of a new meter. Turbines are typically calibrated long to start with, as their calibration degrades with wear. Thus, you will start long, and fall into short readings sometime during the life cycle. But there is no real warning as to when you fall out of calibration as the meter just slows down over time.
Magnetic meters are a pretty good maintenance free choice. They run into turndown issues lower than about 1.5 feet per second, so they aren’t good for gravity returns. But since they are mainly used in pumped systems anyway, turndown is never an issue. Cleanliness of the condensate can be a problem though, as mags will go down to about 10 uFcm before they get into trouble. I replaced one mag this year because the conductivity was not good enough to operate. This also happened at another customer last year, where the mag had worked for years. They hired a new boiler supervisor who cleaned up the condensate, thereby causing the conductivity to fall below 10 uFcm – failing the mag. Truth be known, I’ve provided a ton of magnetic flowmeters to people over the years, but not in condensate. I just don’t like the risk.
So, in essence, if you have the capability of using gravity returns, a gravity meter will save you money on accuracy, pumps, alternators, and electricity. If you are pumping anyway, it’s really up to you. I’ve seen many systems where a gravity is installed before an accumulator as the primary measurement, more than likely based on maintenance costs and accuracy.
With the high cost of energy these days, accuracy may be the sole reason to stay on the gravity side.
Dave